Manufacturing
ERPSirius +Mobile is the most advanced and affordable business tool on the market today. Comprising of an ERP, CRM, MRP II plus other business modules as standard.
ERPSirius MRP helps manufacturing businesses stay organized with accurate production planning and reporting. Provide your customers with an accurate lead time when quoting. Advanced job management and costing, gives you complete information on your production operations.
Improve equipment and resource utilization and efficiency with job sequencing.
Real-time inventory overview prevents stock-outs and lower inventory levels. View inventory transactions, view purchase requirements, and more.
Improve customer satisfaction with precise, on-time deliveries, estimate costs and lead times, shorten lead times and ship promptly.
A complete view of your business, seamless communication between sales, production, warehousing, procurement, administration, transport and shipping, and finance plus more.

Bill of Material (BOM) and BOM Assembly
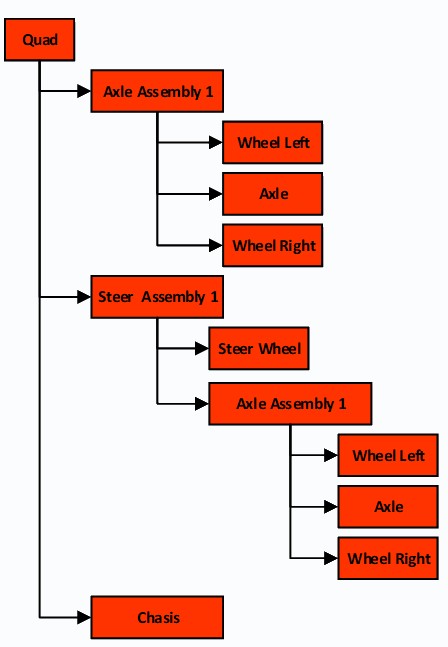
A bill of materials (BOM) is a comprehensive inventory of the raw materials, assemblies, subassemblies, parts and components, as well as the quantities of each, needed to manufacture a product or provide a service that needs parts.
A BOM is the complete list of all the items that are required to build a product. A BOM is sometimes also referred to as a product structure, assembly component list or production recipe (in process manufacturing industries).
Take, for example, a bicycle manufacturer that wants to build 1,000 bicycles. A bill of materials for a bicycle will include all the parts that make up the bicycle such as seats, frames, brakes, handlebars, wheels, tires, chains, pedals and cranksets, including the quantities required of each component and their cost.
A well-defined BOM helps companies:
- Plan purchases of raw materials
- Estimate material costs
- Gain inventory control
- Track and plan material requirements
- Maintain accurate records
- Ensure supply robustness and reduce waste
Types of BOMs
While there are many types of BOMs, some of which are unique to specific business sectors. Assembly BOMs in ERPSirius can be either single-level or multi-level and are highly configurable. The following are the most common for manufacturing and engineering industry:
- Manufacturing Bill of Materials (mBOM)
- The manufacturing BOM (mBOM) is used when a business needs to show all the parts and assemblies required to build a finished product. Parts that require processing prior to assembly are also be included in the mBOM. The document contains information that is disseminated to all the integrated business systems involved in ordering parts and building the product. This included the enterprise resource planning (ERP), materials resource planning (MRP) and, in some cases, manufacturing execution system (MES) of a product.
- The manufacturing BOM (mBOM) is used when a business needs to show all the parts and assemblies required to build a finished product. Parts that require processing prior to assembly are also be included in the mBOM. The document contains information that is disseminated to all the integrated business systems involved in ordering parts and building the product. This included the enterprise resource planning (ERP), materials resource planning (MRP) and, in some cases, manufacturing execution system (MES) of a product.
The mBOM depends on the accuracy of the quantities of parts ordered during the manufacturing process. ERPSirius helps ensure that the purchasing department can maintain the optimal schedule for ordering the necessary parts and negotiate the best possible price from applicable vendors.
- Engineering Bill of Materials (eBOM)
- The engineering BOM (eBOM) is developed during the product design phase and is often based on Computer-Aided Design (CAD) or Electronic Design Automation (EDA) tools. The document usually lists the items, parts, components, subassemblies and assemblies in the product as designed by the engineering team, often according to their relationships with the parent product as represented in its assembly drawings. It’s not unusual for more than one eBOM to be associated with one finished product.
- Service BOM
- The Service BOM (often developed by engineers during the design phase) typically includes a list of all the parts, installation steps and repair instructions that service technicians use when installing or servicing a product onsite at the customer’s place of business.
- Assembly Bill of Materials
- An assembly BOM is similar to a Sales BOM in which the parent item is listed as a sales item and not an inventory item. However, a notable difference is that unlike the Sales BOM, only the finished product appears in the sales document; the children do not appear as sub-items.
- Production BOM
- A Production BOM often serves as the foundation for a production order. It lists the components and subassemblies that comprise a finished product, as well as prices, descriptions, quantities and associated units of measure. During the production process, physical components can be converted into actual finished products. With a fully automated BOM system, component needs, cost, and materials availability can be automatically added to work orders, thus ensuring that raw materials are properly allocated to products.